We're Your Partners in Productivity
A corner cut today is a callback tomorrow. The real path to profitability is productivity. If you need technical support, product recommendations, or good old-fashioned advice, we're here to help.
We exist to help you build something that stands the test of time. To help make you a hero. We do that with high-quality products and world-class customer service.
THE GRABBER DIFFERENCE
Quality
Rigorous testing and high standards means our products will have better consistency and our fasteners will drive faster, seat better, and be less likely to cam-out and spin-out.
Expertise
GrabberPros average more than 13 years with the company, plus many years in the construction industry. We are always ready to show you how to get more from your products and capture real ROI.
Service
A Grabber Professional is ready to serve you where you are, when you need us. Our network can reach 65% of the marketplace in 24 hours and 90% of the marketplace in 48 hours.
Innovation
From our first fastener to our new SuperDrive® Mach1™ collated system, our innovations are designed to help your labor force work smarter and be more productive.
THE GRABBER PRODUCTIVITY PORTFOLIO
We supply more than fasteners. Our product portfolio includes more than 16,000 professional-grade solutions designed to make the lives of contractors and installers easier and more efficient.
LET US SHOW YOU HOW TO INCREASE
PRODUCTIVITY AND PROFITABILITY
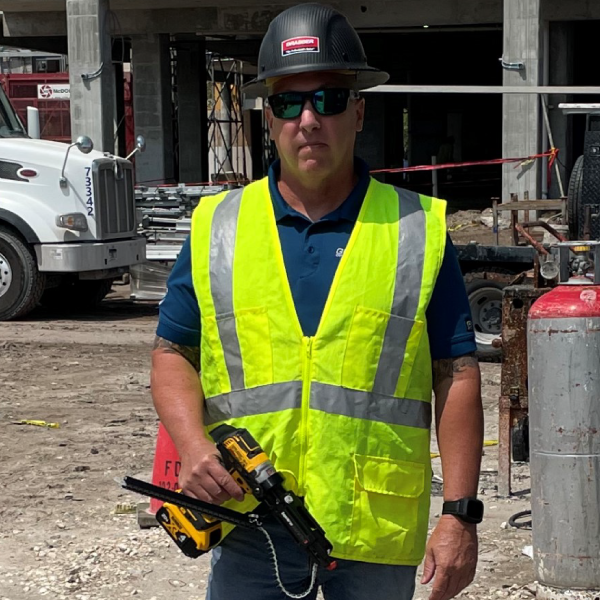
Grabber dealers and professionals are ready to help you find the products and solutions that will make a difference to your bottom line. Because a more efficient workforce means a more profitable business.